A Die Press Die refers to a specialized tool or mold used in manufacturing processes, particularly in industries like metalworking, ceramics, and powder metallurgy. It is an integral component of a die press machine, which is used to shape materials under high pressure. The die itself defines the geometry of the final product by acting as a cavity or form into which material is pressed.
---
●What is a Die Press Die?
A die press die is a hardened steel or carbide tool that serves as the shaping element in a die press machine. It is designed to compress and compact powdered materials (such as metal powders, ceramics, or polymers) into a specific shape. The die typically works in conjunction with punches (upper and lower) to apply pressure uniformly, ensuring the desired density and dimensions of the compacted part.
---
●Key Components of a Die Press System
1. Die (Cavity):
- The main component that forms the external shape of the part.
- Usually cylindrical or custom-shaped depending on the application.
2. Punches:
- Upper Punch: Applies downward pressure to compact the material.
- Lower Punch: Supports the material from below and helps eject the compacted part.
3. Ejector Pins:
- Used to push the compacted part out of the die after pressing.
4. Die Wall Coating:
- A lubricant or coating applied to reduce friction and prevent sticking during the pressing process.
---
●How Does a Die Press Die Work?
1. Material Loading:
- Powdered material (e.g., metal alloys, ceramics, or plastics) is introduced into the die cavity.
2. Compaction:
- The upper punch applies pressure while the lower punch supports the material, causing it to compact and take the shape of the die cavity.
3. Ejection:
- After compaction, the lower punch moves upward to eject the shaped part from the die.
4. Post-Processing:
- The compacted part may undergo sintering (heating) or other treatments to achieve its final properties.
---
●Types of Dies Used in Die Press Machines
1. Simple Dies:
- Used for basic shapes like cylinders or discs.
2. Complex Dies:
- Designed for intricate geometries, often requiring multiple punches or dies.
3. Multi-Cavity Dies:
- Allow simultaneous production of multiple parts, increasing efficiency.
4. Custom Dies:
- Tailored to specific applications or unique part designs.
---
●Applications of Die Press Dies
1. Powder Metallurgy:
- Producing components like gears, bushings, and bearings from metal powders.
2. Ceramics Industry:
- Manufacturing ceramic parts such as insulators, tiles, and electronic substrates.
3. Pharmaceuticals:
- Compacting powders into tablets or capsules.
4. Jewelry and Decorative Items:
- Creating small, detailed objects from metals or ceramics.
5. Automotive and Aerospace:
- Producing high-precision components for engines, transmissions, and structural assemblies.
---
●Materials Used for Die Press Dies
1. Tool Steel:
- Hardened and wear-resistant, ideal for high-volume production.
2. Tungsten Carbide:
- Extremely durable and suitable for high-pressure applications.
3. Hardened Alloys:
- Used for specialized applications requiring corrosion resistance or high-temperature stability.
---
●Advantages of Die Press Dies
1. Precision:
- Enables the production of parts with tight tolerances and consistent dimensions.
2. Efficiency:
- High-speed production capabilities reduce manufacturing time and costs.
3. Versatility:
- Can be customized to produce a wide range of shapes and sizes.
4. Cost-Effectiveness:
- Reduces material waste compared to traditional machining methods.
---
●Challenges in Using Die Press Dies
1. Wear and Tear:
- Repeated use can cause wear on the die surface, affecting part quality over time.
2. Fracture Risk:
- High pressures can lead to cracking or deformation of the die if not properly maintained.
3. Design Limitations:
- Complex geometries may require additional tooling or secondary operations.
4. Material Compatibility:
- Certain powders or materials may stick to the die or cause excessive wear.
---
Square Hydraulic Press Die
●Maintenance of Die Press Dies
1. Regular Cleaning:
- Prevents residue buildup and ensures smooth operation.
2. Lubrication:
- Reduces friction and extends the life of the die.
3. Inspection:
- Periodic checks for wear, cracks, or misalignment.
4. Replacement:
- Timely replacement of worn-out dies to maintain part quality.
---
●Innovations in Die Press Die Technology
1. Advanced Materials:
- Development of harder, more durable materials for longer die life.
2. Surface Treatments:
- Coatings to improve wear resistance and reduce friction.
3. CAD/CAM Design:
- Use of computer-aided design and manufacturing for precise die fabrication.
4. Automation:
- Integration of robotics and sensors for improved accuracy and efficiency.
---
●Conclusion
Die press dies are essential tools in modern manufacturing, enabling the production of high-quality, precision parts across various industries. Their ability to shape powdered materials into complex geometries makes them indispensable in fields like powder metallurgy, ceramics, and pharmaceuticals. By continuously improving die materials, coatings, and design techniques, manufacturers can enhance productivity, reduce costs, and meet the demands of increasingly sophisticated applications.
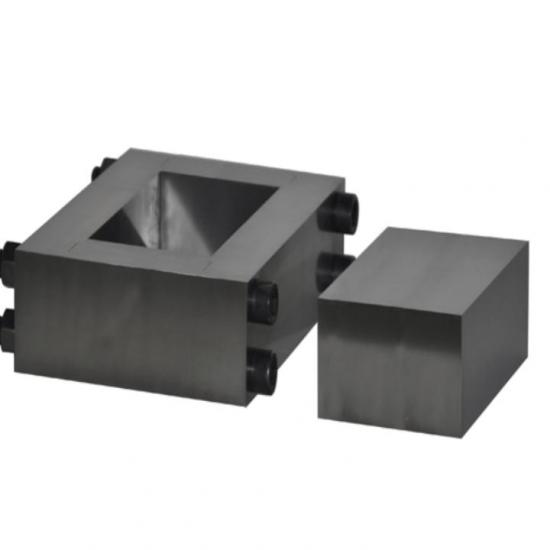